Attic heat recovery in broiler houses
By Jody Purswell, PhD, Agricultural Engineer, USDA-ARS, Poultry Research Unit, Mississippi State and published in MSU Poultry Dept. Spring Newsletter Vol. 1 Issue 1.Fuel use constitutes a large percentage of the energy costs incurred by growers during winter flocks, and increasing fuel costs have illustrated the need to reduce energy usage and improve energy efficiency in poultry production. Researchers at the USDA-ARS Poultry Research Unit and Mississippi State’s Poultry Science Department have been working to determine if using the attic space in a broiler house can be used to pre-heat in-coming air and reduce fuel usage.
Using solar energy to reduce fuel costs in poultry production is not a new idea. Initial research efforts at Penn State started in the 1950’s, and the fuel crisis of the 1970’s spurred further research. However, as energy prices stabilized and poultry housing design improved, solar energy hasn’t received much attention since.
How Much Energy and How Often?
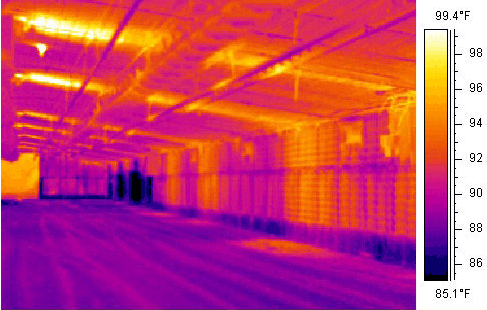
Thermal camera image of the inside of a broiler house with attic vents in the ceiling.
The amount of energy that can be collected in the attic depends on the location, time of day, time of year, construction of the roof, and construction of the attic space itself. For example, at noon on January 1 in Meridian, MS, the solar radiation received is about 270 Btu/h/ft². Taking the area and pitch of the roof into account, the total radiation received is approximately 3.4 million Btu/h. However, not all of that heat will be transferred into the attic – some of it will radiate back into the sky, and some will be taken away by cold air moving across the surface of the roof.
Air temperature was measured in the attic and out-side during brooding for a January 2007 flock. Even though the outside temperature did not exceed 60°F, the attic temperature still reached 75 °F, and stayed warmer than the outside temperature most of the time, even at night. In fact, 79% of the time during the first two weeks of the flock, the attic temperature was between 6 and 14°F warmer than outside.
System Performance
Attic inlets were installed in two houses on a four house commercial farm where the tests took place. Smoke tracers were used to determine the air distribution pattern from the attic vents. The smoke showed a well defined stream of air that traveled along the ceiling to the sidewall with very little drop. Air velocity readings showed greater than 120 ft/min reaching the sidewalls. An infrared camera was used to look at the heat distribu-tion within the house. The thermal image shows the air from the inlet heating the ceiling and sidewalls, as well as the litter where the warm air travels down the sidewall.Gas Usage
Gas usage was estimated from monitoring furnace and brooder run times. Both the brooder and furnace run time were reduced for the house with the attic inlet system, operating 17% and 45% less time than the house with traditional sidewall vents. The house with the attic inlet system used an estimated 108 gal of LP as compared with 142 gal for the house with traditional sidewall vents. The difference of 34 gal of LP would result in a savings of $51.60 per house over the first two weeks of this flock, based on a $1.50 per gallon of LP.
Excessive moisture in the house can lead to problems with ammonia. The difference in moisture between the houses further illustrates the benefit of using preheated inlet air. Under a typical minimum ventilation scenario with one 36” and one 48” fan running every 30 seconds per 5 minutes, the house with the sidewall vents will exhaust 458 lbs of water per day more than the house with attic vents. The estimated energy required to reduce the moisture in the sidewall vented house down to the moisture level of the attic vented house is 494,000 Btu/day, which equates to 5.5 gal of LP gas. At $1.50 per gallon, the cost to reduce the moisture level in the side-inlet house to the same level as the attic-ventilated house will be $8.23 per day.
Conclusion
The preliminary gas usage data shows that the attic system did indeed reduce gas usage, and we are in the process of installing gas meters to determine what the difference in “real world” gas use will be. Additional benefits may be realized from this system by improving air quality during brooding from increased fan run time to offset the increased inlet air temperature. While primarily intended as a means to reduce fuel usage during brooding, the system could potentially provide a means of inexpensively heating the house between flocks to help drive ammonia out of the litter while no birds are present, dry the litter, and reduce the amount of ammonia present when new chicks arrive.
June 2007