Composting Layer Mortalities: Agri-Foods Composter
By Charles D. Fulhage, Department of Agricultural Engineering and Joseph M. Vandepopuliere and Jesse J. Lyons, Department of Animal Sciences, University of Missouri-Columbia - Composting poultry carcasses is a common way for turkey and broiler operators to manage bird mortalities. However, managers of poultry laying operations face their own set of challenges. In turkey and broiler operations, litter is a primary and convenient ingredient in the composting recipe.In laying operations, birds are maintained in cages, rather than reared on the floor. Therefore, no litter is available for the composting process. This publication describes a cooperative field research project between the University of Missouri and Agri-Foods, Hawk Point, Mo. The purpose of the project was to investigate the feasibility of composting bird mortalities in a typical layer operation. See MU publication WQ205, Composting Poultry Carcasses in Missouri, for more detailed information on composting mortalities.
Production facilities
The Agri-Foods layer operation consists of 10 buildings, each housing about 50,000 layers. Mortality averages about 0.75 percent per month, with a 3-pound average bird weight. Daily carcass weight under these conditions is about 375 pounds. Conventional composter design suggests providing 1 cubic foot of primary and secondary composting volume per pound of daily mortality, with an added safety factor of 2.5 to allow for periods of unusually high mortality because of conditions such as heat stress.
These design factors indicate primary and secondary composting volumes of 937.5 cubic feet for the Agri-Foods facility.
Composter
Agri-Foods' compost handling equipment included a skid-steer loader. The bucket size on this loader suggested a minimum composting bin width of 7.5 feet. Primary composting bins were sized at 7.5-feet wide by 6-feet deep by 5-feet high. These dimensions resulted in a volume of 225 cubic feet per bin, and four bins were constructed to provide required primary composting volume. Secondary composting bins were constructed 10-feet wide by 10-feet deep by 5-feet high, with a volume of 500 cubic feet per bin. Four secondary bins were built, for a total of 2,000 cubic feet of secondary composting volume. Extra secondary volume was provided so that compost could be stored for longer periods in the facility and to provide storage for ingredients such as straw. Figures 1, 2 and 3 show details of composter construction.
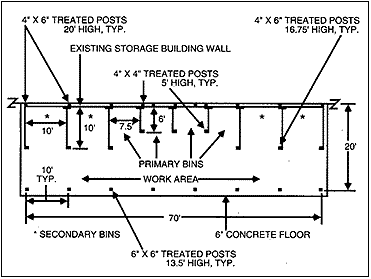
Figure 1: Plan view of Agri-Foods composter.
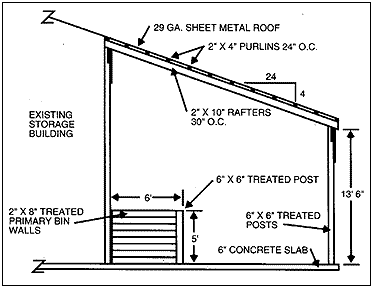
Figure 2: Cross section of Agri-Foods composter showing primary bins.
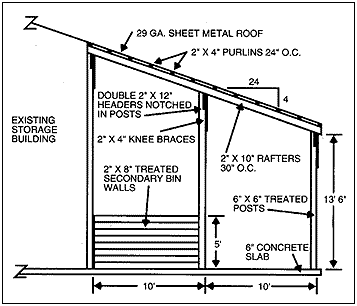
Figure 3: Cross section of Agri-Foods composter showing secondary bins.
Composting trials
The primary objective of the Agri-Foods project was to evaluate the effectiveness of various composting recipes. Wheat straw and fescue hay were used as a carbon source. Also, raw cage layer manure served as a nitrogen and moisture source.
Later, a new recipe using finished compost in place of the carbon source (straw) and raw caged layer manure was tried. Using the recycled finished compost, the primary composting bins reduced fly problems and eased handling because the finished compost was already on-site and does not have to be collected from the layer buildings. Tables 1 and 2 show the ratios of ingredients used in the composting trials. These ingredient ratios resulted in composting temperatures in the 140- to 160-degrees F range in both primary and secondary bins, and finished compost was a dark, dry material with a slight musty odor and very little evidence of feathers or bone.
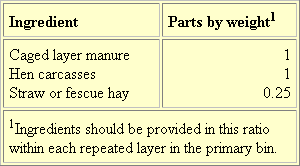
compost to replace caged layer waste.
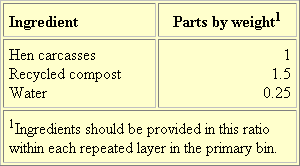
The actual weight of ingredient used in each layer in the primary bin will depend somewhat on bin size and the weight of the carcasses being composted. Based on an average carcass weight of 3 pounds and the bin size used in this experiment, about 50 dead birds, or 150 pounds of carcasses, were added in each layer.
When straw or fescue hay was used as an ingredient, it was most effective to layer half the straw requirement above and below the carcass layer. Based on a 150-pound carcass layer, the straw requirement in these trials was 40 pounds of straw (150 x 0.25 = 40).
Figure 4 is a schematic drawing of the layering scheme used in the trials with straw. Primary bins in all trials were started with a base layer of 6 inches of oak sawdust followed by a one-bale layer of straw. When the primary bins were full, they were "capped-off" with another 6-inch layer of sawdust. With these bin sizes and layering schemes, 17 to 18 layers were required to fill the bin, with 800 to 900 bird carcasses composted in each filling of a primary bin. Normal mortality resulted in filling one primary bin in about one week.
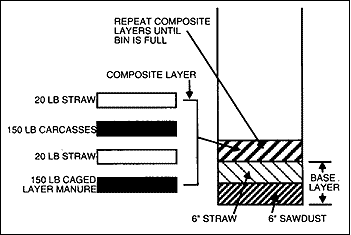
Figure 4: Formation of compost layers using the straw recipe.
When straw was used as an ingredient, it was taken from small square bales. In the trial using fescue hay in place of straw, the fescue hay was "unwound" from a large round bale and placed directly into the primary bins. While the fescue hay trials composted equally as well as the trials using straw, the long fiber lengths of the fescue hay severely hindered bin cleaning when primary composting was completed. Therefore, if hay is used in place of straw, small square bales or round bales that are coarsely ground or shredded with a tub grinder should be used.
Figure 5 is a schematic drawing of the layering scheme using recycled compost in place of caged layer manure and straw. The finished compost in these trials was quite dry, necessitating the addition of water as noted in Table 2. Care should be taken in adding water so that the composting mixture does not become too wet. Water can be added to the layers with a pressured garden hose. However, a hand sprinkler will more accurately apply the required amount of water on each successive layer.
In these trials, primary bins were composted 15 to 20 days before moving the material to the secondary bins. Table 3 shows average values of the chemical content of finished compost in these trials.
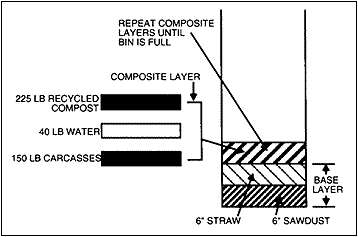
Figure 5: Formation of compost layers using the recycled compost recipe.
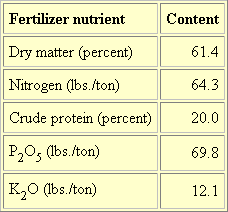
Summary
As of January 1992, the composter at the Agri-Foods facility had been operating for 16 months. During this time, 39,552 hen mortalities were composted. The composting process worked well in both winter and summer. An egg layer operation can successfully initiate composting as a means of managing dead birds by using the ingredient ratios with straw or hay as noted in Table 1. Once a supply of secondary compost is generated, this compost can be recycled as an ingredient to replace both manure and straw as noted by the recipe in Table 2. Water may need to be added because of the dry nature of recycled compost. Refer to MU publication WQ205, Composting Poultry Carcasses in Missouri, for detailed information on poultry composter design, construction and management.
Source: University of Missouri, Columbia - October 1993