“Filières Avicoles” Reports About Major Project in France
FRANCE - The idea for the project came up in the year 2003 - and today, only four years later, the dream is complete. Now 26 and 27-year-old layer farmers Mickaël and David Joubier from Taupont in Brittany recently inaugurated their newly built farm for 150,000 layers with an open day.The impressive large-scale project was described by editor in chief Gérard le Boucher in the cover story of the September 2007 edition of the renowned French professional journal “Filières Avicoles”.
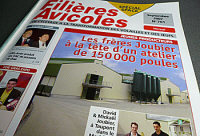
'What a faith in the future!' The journal began. The 25 and 27 year old investors David and Mickaël Joubier recently inaugurated their new layer houses for 150,000 hens with an open day in Taupont in the French department Morbihan. Several hundred colleagues came to take a look at the farm of the egg producers who belong to the Cecab-Group (Cecab: Centrale Coopérative Agricole Bretonne). In a time in which the French egg industry suffers under a fratricidal war between the largest companies of the industry and while the production potential of Brittany wastes away, the inauguration of this exemplary layer farm resembles a silver lining at the horizon.
Big Dutchman was one of the partners of the adventurous Joubier brothers: the German expert company for housing equipment furnished the ambitious project with its enriched Eurovent-EU manure belt battery and the Big Dutchman novelty OptiSec, an innovative manure drying-tunnel.
Learning by doing
![]() |
David and Mickaël Joubier at the packer. |
Laying hen management has been a tradition already on the farm of the parents of David and Mickaël, Daniel and Denise Joubier, in La Moraie close to Taupont. In 1979 they built a small barn for 13,000 laying hens in cages. At the end of 2003 the barn was remodelled and, after reactivation of previously not used production rights, expanded to a capacity of 20,000 laying hens in enriched cages. The future egg producers were also actively involved in the remodelling process. "This was a crucial experience! We took interest in laying hen management and the required investments that are necessary to optimise the production flow" specified the two brothers. And thus they began to plan their own laying hen farm with the support of the Cecab-Group. In 2004 they filed their project petition with the authorities and in the beginning of 2006 all permits were granted.
Almost one year of construction
In the meantime, the Centre de Gestion Agricole and the local bank of Crédit Agricole prepared a feasibility study. The latter financed the project with two credits that have a maturity of 12 and 15 years. And all this despite the still relatively uncommon size of the project: 150,000 laying hens in two houses with egg packer, manure drying-tunnel and manure drying and storage building, require relatively high investment costs.
In the summer of 2006 the earthworks started. The construction was terminated in June 2007 with the paving of access roads to the buildings. The young pullets of the breed Isa Brown from the hatchery Amice Souquet were moved in right on schedule on 17 and 19 July. The farm has a size of 6,000 m², the two laying hen houses have a length of 105 m and a width of 17 m each. The gable, a part of the side wall and the manure storage (900 m²) are cream-coloured, the roof as well as the roof extensions are green. All construction works were carried out by the experienced company Serupa that is located only 30 km from Taupont.
Eurovent EU-system for 60 hens per compartment
![]() |
The EUROVENT EU-system for 60 hens has already proven itself, according to David and Mickaël. |
The two brothers opted for the Eurovent-EU manure belt battery from Big Dutchman as housing system for their hens. The compartments are designed for 60 hens each and thus comply with the directives that will be valid as of 2012. Every house is equipped with six rows, eight tiers and a separate intermediate ceiling. The aisles have a width of 90 cm except for the aisles at the sides which are 110 cm wide.
“The behaviour of the hens kept in a Big Dutchman system that we saw during a visit to the layer farm of Dominique and Corinne Rocher in Questembert convinced us“, explained the Joubier brothers. The system is well-tested and has already proven itself. Furthermore Gérard Rocaboy of Big Dutchman’s French distributor Agromat is a true expert in the layer business according to the two brothers. The system provides at least 750 cm² of surface per bird. The most important features include a double nest with plastic-coated bottom wires and orange curtains, 60 cm2 of free space, four parallel plastic perches, two scratching areas, a claw shortener, Galfan-coated bottom wires and zinc-aluminium coating for a long service life. Nipple drinkers with drip cups supply the hens with drinking water. The hens eat from troughs which are filled by the Champion feed chain.
Dry manure in less than four days
“With regard to the manure drying system we searched for a system which would allow us to achieve a dry matter content of more than 80 percent in just four days — as this remains below the life cycle of flies“ specified the Joubier brothers their decision in favour of Big Dutchman: the manure is removed by means of conveyor belts which transport the manure to the two manure drying tunnels which are located in close proximity to the two layer houses. Fans push large amounts of warm exhaust air through the tunnel. The system is operated without pre-drying of manure. The drying-tunnels from the German supplier have eight tiers, the manure belts have a rather wide width of 1.85 m. The dried manure stays in the manure storage, which is located in the rear of the premises, for one year.
In addition to cross ventilation with exhaust air fans, the company Simatel equipped the buildings with eight fans at the gables. Two Tuffigo Avistar Bus control units steer the house climate and provide ventilating pressure: lateral air inlets (a split baffle and single baffle at the side of the drying tunnel) as well as altogether 25 fans per house.
Modern egg packer
At the rear part of the Eurovent EU-system, the eggs are transported downwards by means of an elevator from where they are transferred to a rod cross conveyor that transports the eggs to the adjacent packer station. The packer area comprises a surface of 500 m² and includes a Diamond farm-packer with a capacity of 72,000 eggs, as well as a robot from the company Ovoconcept. The latter is responsible for the automatic transport of the egg pallets and is also equipped with an integrated weighing device.
Everything else remains in the hands of the young egg producers: The two masters over 150,000 layers have to show the same motivation and commitment in regard to the management of their flock as they already did during the project planning and realization phase. Only then will they be able to achieve a high laying performance. This is certainly a challenge for the two young entrepreneurs, but nonetheless one they will handle more than well!