Automation Aids Traceability
US - It has been rumored for nearly a decade that the Food & Drug Administration is going to require feed manufacturing facilities to be able to trace back ingredients in four hours, but adding to the pressure is customers’ desire to know where their products came from in case of a recall, which requires more from today’s manufacturers, writes Jacqui Fatka.Diamond V kept traceback in mind with its new plant that came on line last fall in Cedar Rapids, Iowa. The company specializes in fermentation products that optimize digestive function and nutrition that are key to animal and aquaculture health, productivity, effi - ciency and profi tability. Fermentation-based technology requires a level of precision. When Diamond V vice president of operations Mike Goble joined the company, he asked his employees their goal, which they said was to make the best feed ingredient product. Goble challenged them instead to make the most consistent product. “You can’t make things better until everyone is doing it the same way,” he explained. Once a level of consistency is reached, then controls and automation provide a standardized method using historical data to determine random variation and, ultimately, reduce the overall variation, Goble noted. There will always be an “art” to growing living organisms, but the company’s goal was to increase the degree of science in the formula from 20-25% to 90-95%. Photo: Diamond V. TRACEABILITY: Diamond V’s new Cedar Rapids, Iowa, facility has 32 raw material storage bins that each hold only one truckload to increase confidence in its ability to track products.
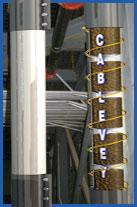
Automation Advantages
Rather than adding more people, Diamond V and many other plants are adding automation to reduce the potential for human error. Many automation systems rely on human input to maintain system controls, Goble said, but Diamond V has gone one step further, allowing automation to input information.
Each ingredient load received is scanned at arrival and instantly entered into the computer system rather than requiring employees to enter the information. At Diamond V, automated controls talk to the operators at every level of operation. Unless the entered command meets certain parameters, it will not continue.
Fred Olson, software engineer for Beta Raven, a subsidiary of CPM, explained that automation is key to traceability. Without it, the only way to track and trace product is for the operator to write down whatever lot is used to make each batch. In addition, faster computers allow programmable logic controllers to be integrated to turn on augers, turn heads, etc., Olson said. More and more of the plant can be automated. Each and every step along the way requires traceability. “One day, the plant manager will fi ll in schedules and turn on a switch, and the plant will just do it. We’re not there yet, but that’s the goal,” he said.
Automation and computer advancements have also allowed more support to be done online. Olson said the number of service trips the company makes today is one-tenth as many as just fi ve years ago due to the ability to connect directly to customers and make needed changes to hardware and software. Furthermore, this online capability lets mill managers remotely conduct trackand- trace investigations.
Given constant demands to be faster, cheaper and more controlled, lost production is costly, Olson added. Diamond V does periodic mock recalls at its Cedar Rapids facility to help prepare employees. Customer audits also require the company to go through the steps of tracking product. Prior to the automated system, it took six people three hours to find maybe around 98% of the product. Now, it takes one person 20 minutes to fi nd 100% of what is in each bag that leaves the facility.
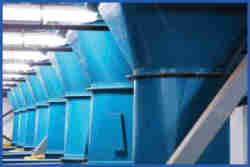
Facility Features
The new Diamond V facility was designed with traceability in mind. For instance, Goble noted that the facility has 32 storage bins instead of 8-10, and each holds only one truckload of ingredient material. This allows management to confi - dently know which lot is for which load. “It added additional capital up front but provided a higher integrity for traceability and tracking,” Goble said.
Another key component of the facility is the food-grade system. Complete segregation from one product to another is needed after changeovers. Goble said the plant was designed to facilitate changeovers by using a Cablevey tubular system instead of traditional mechanical transfer systems. Cablevey systems allow for complete cleanout between products and eliminate concerns about carryover.
Partnering
Diamond V doesn’t produce foodgrade products but maintains a food-grade status and even invites in food inspectors to get ideas on how to improve its facility and set the bar higher.
“Our philosophy is steady, continuous improvement. This helped us seek answers on how we can improve value and do a better job overall — not just meet the minimum standard,” Goble said. When designing the new facility, the company took into consideration where to store products in the warehouse, particularly how close items were to the walls. It also made lighting considerations to avoid dark corners.
On the customer side, Goble noted that Diamond V wants to supply the industry with both product and service. It has an open-door policy and invites customers to visit as often as they’d like; it also encourages customer audits. “We don’t just want to have a customer; we want them to be an extension of us,” Goble said.
Diamond V partners with its suppliers as well. Instead of looking for the lowest price, it may end up paying a bit more to get higherquality products and service. As Goble explained it, “We expect the best value, which may not always be the lowest price.”
* This article appears in Feedstuffs June 7, 2010 issue, page 13