Small-Scale Egg Handling - 1
A guide to the production and sale of eggs for small-scale and free-range egg producers published as Small Scale Egg Handling by ATTRA, the US National Sustainable Agriculture Information Service. This first of three parts covers egg production to minimise dirty eggs as well as methods of egg cleaning and grading.Summary
Many small-scale egg producers sell specialty eggs, such as free-range or organic eggs, to the public at farmers’ markets and other venues and need to wash the eggs or prepare the eggs for market. Immersing or soaking the eggs in water is not recommended, but small- and medium-scale egg washers that use brushes and sprayers are very expensive. Small producers often use low-tech methods to clean eggs, including dry cleaning, dipping and spraying or pouring. Small producers should also candle and grade eggs to ensure high quality.
Introduction
While information on large-scale egg washing and handling is readily available, there is less information available on handling eggs on a small or medium scale. This publication covers proactive methods to keep free-range eggs clean through egg collection, egg cleaning, candling and grading. You should be aware of your local regulations on the sale of eggs so you will know what practices are required. Information on substances approved for use in organic production and equipment suppliers is listed in the Further resources section.
For information on producing eggs in alternative and free-range poultry production systems, see ATTRA’s Alternative Poultry Production Systems and Outdoor Access.
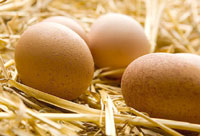
Keeping Eggs Clean
Egg washing is an important issue in alternative poultry production systems because eggs often become dirtier in free-range systems than in cages. Dust, mud, faeces, feathers and contents from broken eggs may soil as many as 30 per cent of eggs in free-range systems (Parkhurst and Mountney, 1988).
Free-range systems should minimise mud on pastures and make provisions such as pallets, straw or gravel at the entrance of the bird doorways to clean the feet of hens entering the poultry house. It is also important to maintain clean nesting material. If eggs are broken in the nest the other eggs will get dirty.
Methods to prevent broken eggs include collecting eggs often, using a nest with a sloping floor (roll away nest) so that eggs roll to a separate collection area and allowing access to the nests only during the morning when most birds lay. Hens should not sleep in nest boxes because the hens will defecate. That dirties the eggs and prevents them from rolling out, increasing the potential for breakage. Some nest boxes have a grill or door to keep birds out during the night, and sufficient perch space will allow birds to roost at night rather than sleep in nest boxes. Provide a sufficient nest area to prevent hens from laying eggs on the floor where the eggs are easily soiled. If individual nest boxes are used, allow no more than 5 hens per nest box. If communal nest boxes are used, follow the manufacturer’s recommendations.
The Freedom Food program in the UK allows one square metre for 120 hens in communal nest boxes. This can be calculated as 11 hens for a square foot. Nests should be designed or oriented to allow birds to avoid brightly lit areas during lay; some nests use curtains for darkening.
Egg collection
In laying operations, most of the eggs are generally laid within five hours of the first light in the morning. Collect eggs often — twice in the morning and once in the afternoon — to help decrease the number of dirty and broken eggs and start cooling eggs (Bigbee and Froning, 1997). Collection should be more frequent in very hot or cold weather. Eggs should be held at 60°F and 70 per cent relative humidity before cleaning. Eggs stored at room temperature, about 75°F, can drop as much as one grade per day. Embryos can start to develop in fertile eggs held at a temperature above 85°F for more than a few hours (Parkhurst and Mountney, 1988).
Keep egg temperature relatively constant until the eggs are washed to avoid sweating. Sweating occurs when eggs are moved from cold storage to a warm environment. Condensation on the surface of the egg facilitates the movement of microbes inside the shell due to moisture. In the past, eggs were held in plastic-coated wire baskets so that the air could circulate freely among the eggs and cool them. Now, eggs are also held in fibreboard flats that hold 30 eggs per flat. Misshapen, cracked, broken or extremely dirty eggs should be separated from clean eggs.
Manual egg gathering is labour-intensive. An egg cart, filler flats and a nearby storage site will help reduce labor. In mechanised egg collection, a moving belt brings the eggs to a section of the house where the eggs can be packed into flats. Eggs are positioned in the flat with the small end down, the same position they should be in the carton as well. Roll-away nests simplify egg collection because the eggs can roll from the sloped floor of the nest to a collection area or belt.
Eggs are ideally packed within 24 hours after they are laid. US Department of Agriculture (USDA) rules require that eggs be packed within 30 days of lay. In programs that assure high quality, eggs are usually packed within three to seven days of lay. It is important to remember not to store eggs in coolers with items that give off odors, such as onions and citrus, because the eggs can pick up the odor through the shell’s pores.
Cleaning
Eggs are cleaned to remove debris and stains and reduce the microbial load. Excessively dirty eggs should not be cleaned, but rather discarded.
Dry cleaning
A slightly dirty egg can be brushed with an egg brush or rubbed with a sanding sponge and sandpaper.
Wet cleaning
Naturally, the egg has good defenses to help protect the embryo during incubation. The shell is covered by a waxy layer (the cuticle) that helps prevent microbes from entering the pores that allow the passage of gases. The cuticle is not impenetrable and water on the surface of the egg shell can undermine these defenses because water helps bacteria pass through the shell pores into the egg. If the period of contact between egg and water is short, there will be little microbial penetration into the egg (Zeidler, 2002). Therefore, it is important to limit the amount of time that the shell is wet. Soaking eggs in water for as little as one to three minutes can allow microbes to penetrate the shell (Zeidler, 2002).
Although the USDA does not allow immersion washing (allowing eggs to stand or soak in water), most small producers are not operating under USDA requirements. Most operate under exemptions to state egg laws and washing methods are usually not specified. Small-scale egg washing should take place with a continuous flow of water, such as dipping, spraying or pouring, that allows the water to drain away from the eggs.
Only potable water should be used for cleaning. According to the USDA, iron levels in the water must not be higher than two parts per million (ppm). Egg white does not contain iron and this helps prevent microbial growth but if iron is introduced it may induce spoilage of the egg contents (Zeidler, 2002).
Interestingly, in Europe Grade A eggs are not washed. This practice is a result of research done in the early 1900s that indicated washing eggs before storage resulted in unpredictable and sometimes deleterious results. However, the length of wash time, cleanliness and temperature of the water and the proper use of sanitizers varied widely in these studies (Hutchison et al., 2003).
Note that washing eggs can damage the cuticle or bloom, the waxy layer that seals the pores and helps keep out bacteria. Older egg production books do not recommend washing eggs at all. In the past, it was important to protect the cuticle because refrigeration was not always possible.
Pre-wetting
Wetting or lightly spraying the eggs with warm water, about 104°F, prior to washing will help loosen debris on the shell (Hutchison et al., 2003).
Washing
Eggs should be washed in water that is at least 20°F warmer than the warmest eggs, and the water should be at least 90°F. This is to prevent water that is cooler than the egg from forcing the egg contents to contract and pull water and microbes through the shell into the egg and cause contamination. However, the wash water should not be more than 40°F above the temperature of the eggs or the eggs may experience thermal cracking.
Cleaners can be helpful in the washing process. According to the Food and Drug Administration (FDA) the ingredients in the material used to clean eggs must be Generally Recognized as Safe (GRAS). The ingredients must also be a substance that is regulated as a food additive (USDA FSIS, 2008). Ingredients in compliance with FDA guidelines can be found in the Code of Federal Regulations. Detergents help remove dirt and kill microbes during wet cleaning. Detergents generally raise water pH to 11 and the alkaline environment helps kill microbes, including salmonella (Zeidler, 2002). There are many detergents or egg soaps on the market. For example, Egg Wash Powder is an alkaline chlorinated foam controlled powder available through Incredible Egg Washer Co., Nasco and other suppliers.
In certified organic processing under the National Organic Program, §205.605 of the National List lists non-agricultural (nonorganic) substances that may be used in processed products labeled as organic or made with organic ingredients. The list includes natural materials such as citric and lactic acids and synthetic materials including chlorine, hydrogen peroxide, ozone potassium hydroxide, and peracetic acid. The Organic Materials Review Institute (OMRI) lists brand name products that are allowed under this National List. The name brand list includes AFCO 5242 Egg Wash Org, whose main ingredient is potassium hydroxide. Keep in mind not all possible options are listed because there is a cost for OMRI listing.
Be conscious of where your wash water goes, as ongoing and excessive use of detergent could be harmful to your septic system. If you dispose of wash water on farm, a gentler soap or other material should be used. IPS-CareFree Enzymes, Inc. has an egg wash product called Egg Washer Pro that breaks down contaminants with a blend of enzymes that make up the wash. Some small producers use a solution of distilled white vinegar diluted in half with water to wipe their eggs. Vinegar can aid in removing stains from the shell and is known to have antibacterial properties due to its acidity (Entani et al., 1998).
The USDA requires that wash water be changed every four hours in commercial production. Replacement water is added continuously.
Defoamers are used with egg-washing machines to help reduce foaming. Excessive foaming causes water to spill over sides of tank and this affects water temperature and pH.
Rinsing
Eggs are rinsed to remove adhering dirt, detergents, and foam (Zeidler, 2002). Rinse water should be a few degrees higher than the wash water to prevent drawing the water into the egg.
Sanitising
After washing, eggs are sanitised to reduce microbial load.
Chlorine-based sanitisers should be from 50 to 200 ppm (Zeidler, 2002). However, using less than 100 ppm chlorine may help protect the cuticle (Hutchison et al., 2003). One tablespoon of household chlorine bleach, usually 5.25 per cent sodium hypochlorite, per gallon of water will result in a solution of 200 ppm chlorine (McGlynn, 2009). Free chlorine level must be frequently checked because chlorine is inactivated by organic material such as dirt. Chlorine test strips are available in restaurant supply stores.
Organic requirements permit a final rinse with a chlorine level less than 4ppm, the limit under the Safe Drinking Water Act. See the OMRI product list for approved sanitisers and check with the individual company to ensure the product can be used on shell eggs.
Interestingly, in a test comparing the effectiveness of sanitisers including chlorine, electrolysed water and peracetic acid, none of the sanitisers were more effective than rinsing with water (Musgrove et al., 2008).
Drying
Eggs should be dried after washing and before packing and storing to prevent fungal and microbial growth. Eggs can be dried by evaporation, with fan assistance or by wiping.
Candling
In some states, small-scale producers may be required to candle eggs to ensure interior quality of the eggs in terms of blood spots, cracks and more. Even if you are exempt, candling is still important to ensure your customers do not receive fertile eggs with developing embryos, eggs with blood spots or cracked eggs. If you gather frequently and use cold storage, embryos will not have the chance to develop in fertile eggs.
Brown eggs are more difficult to candle than white eggs due to the darker shell which can generally lead to a higher percentage of blood and meat spots.
Grading
Grading involves sorting eggs based on quality, size and weight standards. Quality is based on shell quality, the air cell, the white and the yolk. For example, the highest quality Grade AA has a clean, unbroken, unstained shell; the air cell is 1/8 inch or less in depth; the white is clear and firm; and the outline of the yolk is only slightly defined and free from defects such as blood spots. The USDA Egg Grading Manual describes how grading is done under the USDA (USDA, 1990).
Grading also involves sorting eggs into weight classes or sizes including peewee, small, medium, large, extra large and jumbo. The USDA Egg Grading Manual explains the required individual egg weight and how much a dozen eggs need to weigh for each weight class. Consumers notice size variation within a carton but not as much from carton to carton. Most states do not require small-scale egg producers to grade eggs and cartons usually must be marked as ungraded.
November 2009