US Poultry Industry Manual - Broilers: Grow Out
Grow out is the second stage of broiler growthPart of Series:
< Previous Article in Series Next Article in Series >
Editor's Note: The following content is an excerpt from Poultry Industry Manual: The Foreign Animal Disease Preparedness and Response Plan (FAD PReP)/National Animal Health Emergency Management System (NAHEMS) Guidelines which is designed to provide a framework for dealing with an animal health emergency in the United States. Additional content from the manual will be provided as an article series.
Grow-out, the second stage of broiler growth, begins when the house dividers are removed and chickens move into the entire house. This period typically begins at 11-16 days of age and continues until the broilers are removed for processing. During grow-out, broilers are no longer as fragile and not quite as susceptible to disease or changes in temperature. However, care must continue in the grow-out stage to enable the broilers to reach their maximum potential.
Feed
Feed is the largest single cost in broiler production. Broiler chicken feed consists largely (about 85 percent) of corn and soybean meal. There are no major differences in nutritional requirements between broiler strains but goals of a nutrition program may differ between production companies. Rations formulated by poultry nutritionists may be designed to attain maximum profitability of live birds or they may be designed to optimize yields of certain carcass components, such as breast muscle. High energy rations optimize live weight gain and feed conversion but may result in higher carcass fat content and a higher incidence of metabolic disorders. Diets with optimal crude protein and amino acids may produce slower weight gains and poorer feed conversion but yield more lean muscle in carcasses. Formulation of broiler rations is influenced by availability of raw materials and their cost, age and sex of chickens in the house, and desired live weights at slaughter. Furthermore, rations may be modified during periods of high ambient temperature to minimize heat stress or reduce environmental contamination associated with nitrogen and/or phosphorus excretion. In 2012, average cost per ton of feed was $347. Average feed cost per pound of broiler meat was $0.31.
Soybean meal is the major source of protein and amino acids in poultry feed throughout the world. The amino acid profile of soybean meal is excellent for chickens. Protein and amino acids are absorbed from the gut and are primary constituents of skeletal muscle, feathers, bone matrix, ligaments, skin, nerves, and organs. Feeds are often supplemented with synthetic amino acids, such as methionine, lysine, and threonine, to satisfy requirements for growth-limiting amino acids. Sulfur-containing amino acids, such as methionine, are the first limiting amino acids in broiler feed because they are used for feather growth, which has priority over muscle growth. Lowering feed costs by lowering protein levels may result in deficiencies of one or more amino acids and reduction in breast meat yield. Corn and wheat are primary sources of energy-producing carbohydrates in broiler diets with lesser amounts of energy coming from fats or oils. Energy is needed to support rapid growth, maintenance of body tissues, and activities of the birds. A vitamin-mineral premix is used at varying levels throughout the life of broiler chickens. Vitamins include fat-soluble (A, D, E, and K) and water soluble vitamins (B-complex and C). Limestone and oyster shell are sources of calcium, which is needed for formation of bones, blood clotting, and intracellular communication. Phosphorus is required for bone formation, energy transfer, and phospholipids. Potassium, sodium, chloride, and magnesium work with phosphates and bicarbonates to maintain correct levels of osmotic pressure and pH. Trace minerals are part of larger organic molecules involved in many metabolic reactions and include iron, iodine, copper, manganese, zinc, and selenium.
Enzymes are used in broiler chicken feed to improve digestibility of feed ingredients. Phytate phosphorus accounts for 60-70% of phosphorus in plants and is poorly digestible. Phytase is widely used in broiler chicken feed to release phosphorus bound to phytic acid in plant materials. Inorganic phosphorus is expensive to purchase and using phytase lowers feed costs by lowering the amount of inorganic phosphorus needed in the ration. In addition, phytase has a positive effect on the environment by reducing the amount of phosphorus excreted in droppings. Other enzymes can be employed to improve the digestibility of carbohydrates in cereals grains. Wheat, barley, sorghum, oats, and rye contain non-starch polysaccharides (previously called fiber), which become more digestible after the addition of appropriate exogenous enzymes to the feed. New enzymes that are not destroyed by heating and can be added to the feed before pelleting are being developed.
During the grow-out period, feeding programs attempt to optimize body weight uniformity, feed efficiency, average daily gain, and livability. As the broilers grow, each successive diet has a lower level of protein and a higher level of energy. Changing nutrient requirements as broiler chickens age are satisfied by providing separate grower, finisher, and withdrawal feeds in the form of pellets, larger particles that deliver more volume per bite. The change from crumbles to a pellet diet is initiated by the integrator who supplies the feed. Each pellet provides a complete nutritional package when eaten. Pelleted feeds are easier to handle and produce better feed efficiency and growth rates than mash feeds. High temperatures during pelleting reduces bacterial levels in feed by 5 to 10 times, however, spore-forming bacteria are not completely inactivated. Grower feed is given to broilers for 14 to 16 days after the starter feed. It has the highest nutrient density, which supports maximum growth rates. Finisher feeds are given from approximately 25 days of age until processing and account for the major volume and cost of feeds ingested by broiler chickens. Using least cost feed formulation is important when designing finisher feeds to maximize financial returns. Withdrawal feeds are fed for a sufficient period of time prior to slaughter (usually around 5 days) to meet federal drug withdrawal requirements for antibiotics, growth promoters, or coccidiostats so drug residues do not occur in broiler chicken tissues following processing.
Water
Water is an essential nutrient for digestion that should be continuously available. Approximately 70% of a broiler’s body weight is water, of which 70% is intracellular and 30% extracellular. Providing sufficient, clean water is critical to a flock’s success. Water should not contain excessive amounts of minerals, bacteria, nitrates, or nitrites. Water consumption increases with bird age and ambient temperatures and is influenced by relative humidity and diet composition. Excessively warm water reduces intake so flushing water lines during hot weather helps to provide cool water and encourage water consumption. Broiler chickens in temperate climates drink approximately twice as much water as feed consumed on a weight basis. Water consumption rates shown in the table below were derived from those published by Leeson and Summers in the book entitled Commercial Poultry Nutrition (3rd edition).
Table 11. Daily Water Consumption of Broiler Chickens (gallons/1,000 birds) |
||
Age (Weeks) |
Ambient Temperature |
|
68°F |
90°F |
|
1 |
6.3 |
10.5 |
3 |
26.2 |
50.0 |
6 |
62.9 |
131.0 |
9 |
78.6 |
157.0 |
Light
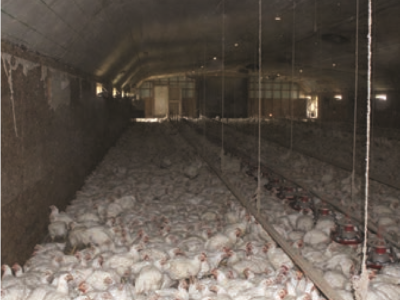
Lighting programs for broiler chickens during grow-out are either restricted or intermittent. Restricted lighting programs use a daily photoperiod of about 18-20 hours of light with 4-6 hours of darkness during a 24 hour day, depending on the desired live weight at slaughter. Numbers of hours of light available each day and the light intensity affect bird behavior and activity. A light schedule should provide adequate dark time for broilers to rest, but be short enough to prevent lengthy periods when the flock is without feed. Feed takes approximately 4 hours to pass through the intestinal tract of broiler chickens. Aggressive feeding behavior resulting in skin scratches, which predispose to infectious process and increased condemnations at processing, occurs when the birds do not have feed for more than 6 hours. Periods of darkness longer than 6 hours exacerbate problems associated with high stocking densities and limited feeder space. In addition, too much light exposure may cause increased activity of broiler chickens and lead to carcass bruising, infectious process, and poor feed conversion. After chicks are released from the brood chamber and have spread uniformly throughout the house, light intensity may be dropped to about 0.5 to 1.0 foot candle (5-10 lux). A dimmer switch can be used to gradually increase light intensity over a one hour period after lights come on in the morning and slowly decrease light intensity over a one hour period before lights go off in the evening.
Intermittent lighting programs often use 6 cycles of one hour of light followed by 3 hours of darkness in a 24 hour day.
Temperature
Heating and cooling the house is an essential part of raising broiler chickens. Average house temperatures must be reduced as broiler chickens age because rapidly growing chickens generate substantial amounts of heat throughout the house. In the case of a ventilation failure, death results from overheating rather than inadequate oxygen. Instead of supplying heat, as occurs during brooding, heat removal becomes more critical. Older birds are more difficult to keep cool because they are better feathered and insulated and generate significant amounts of body heat. Broiler chickens remove excess body heat through sensible and latent heat loss mechanisms. Sensible heat loss occurs via convection, radiation, and conduction. Latent heat loss takes place by evaporation of water from the respiratory tract. In summer, approximately one third of body heat lost by broilers occurs from sensible heat loss and two thirds from evaporative cooling via panting. Once birds begin panting, efficiency of body weight gain and feed conversion are sacrificed.
Therefore, the closer poultry producers maintain ideal temperatures during summer heat, the better bird performance.
The majority of broiler houses have computerized environmental controllers that control temperature based on feedback from thermal sensors. Environmental controllers activate fans, side-wall inlets, tunnel ventilation, evaporative cooling pads, and curtains as needed to achieve the desired temperature. Foggers, evaporative cooling pads, and sprinklers are frequently used to cool houses and birds in summer. During hot weather, tunnel ventilation allows for maximum airflow in a house. To prevent temperature build up, air speeds for older birds in a house should be around 500 to 600 ft/min. Air movement at this speed creates a wind-chill effect and pulls trapped heat from between the chickens. Air is drawn into the house through evaporative cooling pads, which further aids in maintaining house and bird temperatures. Insulation is of great importance to prevent transfer of radiant heat from the roof to the broilers. While the cost of insulation is quite high in parts of the world, it is still more effective than over-sizing ventilation and cooling systems.
High relative humidity on hot days impairs the efficacy of evaporative cooling by the ventilation system and reduces heat loss through evaporation of water off the birds’ respiratory system, which can result in high mortality. Conversely, if relative humidity is low and house conditions are dusty, respiratory problems, airsacculitis, poor feed conversion, and poor weight gains are likely to occur.
Ventilation
Modern broiler houses use power tunnel ventilation and have solid side walls, roof insulation, evaporative cooling pads, and fogging systems. Automated systems control house temperature and monitor static pressure, air velocity, and negative pressure. Computer controllers can be programmed to adjust the minimum ventilation rate as birds age so that adequate moisture and gas removal occur even during cold conditions. Tunnel ventilation systems have air intakes at one end of a house and exhaust fans at the other end. Negative pressure is created within air-tight houses by turning on electric exhaust fans that draw air out of the house. The speed at which air enters the house is determined by the vacuum created within the house and the size and shape of air inlets. Typically, air is drawn through the length of a house at the rate of about 500 feet per minute, which creates a wind-chill effect and lowers the effective temperature by about 10o F. Tunnel ventilation, when combined with evaporative cooling pads and fogging systems, effectively cools broiler chickens during periods of intense summer heat unless the humidity is also high. With evaporative cooling, air is drawn through wetted cellulose pads and energy released during evaporation reduces the temperature of air entering the chicken house. Fogging systems cool incoming air by evaporation of water that has passed through fogger nozzles.
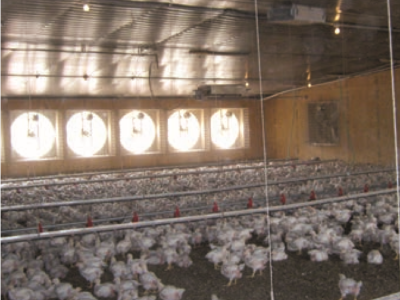
Older chicken houses use natural ventilation, usually lack insulation, and have curtains on the sidewalls that can be raised or lowered. Natural ventilation consists of air currents that enter one side of a house, pass over broilers in the house, and leave through the opposite side wall. The rate of air exchange depends primarily on outside winds and sidewall fans that are used to improve air circulation and help create a wind-chill effect. In older houses without automated control systems, growers must adjust curtains several times a day to optimize ammonia and moisture removal and still maintain good growing conditions. On hot summer days, curtains are lowered to allow more outside air to enter the house and foggers or misters are used when further cooling is needed. In addition, circulation fans can be used to increase air speed at bird level. During cold weather, curtains are raised to limit the flow of air into a house and circulation fans are used to mix incoming cold air with warm air in the house.
Ventilation is used to remove heat from broiler houses during summer and to remove moisture from broiler houses during winter. A flock of 20,000 seven-week-old broilers produces approximately 500,000 British Thermal Units (BTUs) of heat each hour in a chicken house. In addition, on hot days, heat entering a house through the ceiling and side walls may add another 150,000 BTUs. If excessive heat is not removed, broiler chickens may die. The air exchange rate during grow-out should be double the air exchange rate during brooding. Exhaust fans controlled by a timer, not by a thermostat, pull hot air out of broiler houses and may completely exchange the air in one minute. In cold weather, minimum ventilation is maintained to bring fresh air into houses and prevent moisture build up. Air exchange may occur once per minute in 3-6 minute cycles, which will optimize air quality without over chilling the air.
Litter
Over time, litter builds up and gradually decreases in quality. As chickens age, they excrete larger amounts of waste that accumulates resulting in litter becoming “caked”, or clumped. As much as 100 tons of litter and excreta can be produced during the course of a year from 6 flocks in a 40’ by 400’ house. Due to the shortage of bedding material available to the industry, it is a common practice for producers to reuse litter (bedding plus excreta) for a year or longer, a process referred to as using “built-up litter”. Composting built up litter between flocks helps reduce pathogens, parasites, and insect pests that can carry over in the litter from the previous flock.
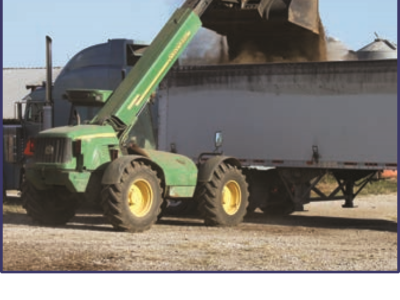
Mortality
In the first week, mortality may be around 1% but should decrease to 0.5% or less during the second week. Through weeks 3 and 4, mortality should remain very low. It may slowly increase from week 5 through the end of production. Typically, 6-week-old flocks of broiler chickens go to market with only 2-4% mortality during the life of the flock. Average mortality of broiler flocks between placement and processing was about 3.6% in 2011 in the United States.
It is vital to be conscious of bird health throughout grow-out, especially towards load-out. As birds approach market age, high mortality greatly increases financial loss because a substantial amount of labor and feed have been put into growing these older chickens. The greatest economic loss comes from birds condemned at processing. Mortality must be monitored daily and dead birds promptly removed from the house.
Culling
Culling to remove sick chickens is important in preventing or limiting disease outbreaks. Growers should walk houses daily to check for sick and dead birds, record their number, and dispose of carcasses properly. Broiler chicks that have crossed beaks, show signs of illness, cannot stand to eat or drink, are blind, or are excessively small should be culled. These chicks consume feed and water but are likely to die and spread disease. Culling birds on the farm prior to load-out helps reduce losses from condemnation at processing. Chickens to be culled are usually killed by cervical dislocation or carbon dioxide gas.
Carcass Disposal
Disposal of dead birds is regulated by local, state, and federal governments to control the impact of carcass disposal on air quality, water quality, and the spread of disease. Disposal of mortality is a daily necessity since dead birds can harbor pathogenic microorganisms with potential transmission to other poultry. Cost of supplies, labor reliability, maximum anticipated daily mortality, and degree of biosecurity associated with each method must be assessed.
Carcass disposal methods include composting, rendering, burial, and incineration. Burial has been banned in most states due to the risk of contaminating ground water. Most states allow on-site or landfill burial through permit only and only under catastrophic conditions. Incineration is the most biologically safe way to dispose of dead birds. It does not negatively impact water quality when ash is properly handled and does not contribute to problems with disease, insects, or vermin. However, incinerators must be properly designed to avoid odor problems and should be located down-wind from residences and other poultry houses. Because of fuel costs, incineration tends to be expensive.
Composting is popular because it is inexpensive to manage and, when done properly, creates an environmentally friendly, pathogen-free fertilizer. Composting requires construction of a solid floor and covered roof system that has adequate primary and secondary bin capacity to meet the predicted mortality level for the farm. Composting is achieved by providing a mixture of carbon, nitrogen, air, and water to encourage microbial growth. A carbon to nitrogen ratio of 25-40:1 is created by layering litter and other organic material, such as straw, with moisture-rich carcasses. The level of moisture in the composting material should be 40-60%. Addition of air by turning the material at set intervals creates the perfect recipe for natural aerobic breakdown of organic materials. In properly constructed piles, temperatures are expected to reach between 120 to 160°F within the first 10 days. It is generally thought that 1 to 2 days at 149°F is sufficient to inactivate pathogens. Once the compost temperature begins to drop below 55°F, it should be aerated by turning the pile or moving composting material to a secondary bin. Composting requires 16 to 20 days for the first heat cycle and roughly the same amount of time for the second heat cycle. Major drawbacks to composting are construction and labor costs, since the system requires careful and frequent management.
Rendering is the process of mechanically processing carcasses to reduce tissue size with subsequent cooking and further refinement resulting in the formation of a carcass meal. Rendering was once a popular method of carcass disposal because dead birds were processed into a value-added, protein-rich feedstuff that could be added into poultry feed or pet food. Rendering has now fallen out of favor, primarily because of biosecurity issues and high fuel costs. Movement of rendering trucks handling dead birds and moving from farm to farm has been identified as a risk factor for spreading diseases, such as avian influenza. Significant costs are associated with transporting carcasses to rendering facilities.
Reference: "USDA APHIS | FAD Prep Industry Manuals". Aphis.Usda.Gov. 2013. https://www.aphis.usda.gov/aph...
The manual was produced by the Center for Food Security and Public Health, Iowa State University of Science and Technology, College of Veterinary Medicine, in collaboration with the USDA Animal and Plant Health Inspection Service through a cooperative agreement.