US Poultry Industry Manual - Broilers: breeding flocks
Part of Series:
< Previous Article in Series Next Article in Series >
Editor's Note: The following content is an excerpt from Poultry Industry Manual: The Foreign Animal Disease Preparedness and Response Plan (FAD PReP)/National Animal Health Emergency Management System (NAHEMS) Guidelines which is designed to provide a framework for dealing with an animal health emergency in the United States. Additional content from the manual will be provided as an article series.
Primary Breeders
Primary breeding companies are large international enterprises with geneticists, nutritionists, veterinarians, and computer specialists on their staffs. Today, there are only three major primary broiler breeding companies in the world – Cobb-Vantress, Aviagen, and Hubbard. Cobb-Vantress incorporated the Hybro breed in 2007 and focuses on selection for feed conversion because feed is the single largest cost associated with producing broiler chickens. Aviagen’s product portfolio includes Ross, Arbor Acres, and Lohmann Indian River (LIR) brands. Aviagen is the largest broiler breeding company in the world with 44% of global market share and operates in over 85 countries. Hubbard is owned by Groupe Grimaud, the second largest multi-species animal breeding company around the world. Hubbard has a presence in nearly 100 countries and offers a range of genetic products to meet specific needs for different market segments.
Primary breeding companies increase the genetic potential of broiler chickens by selecting for traits that improve production efficiency, such as rapid growth rate, feed efficiency, and breast meat yield and quality. Broiler breeding programs rely on quantitative genetics, computer science, and DNA chip technology to select breeding birds. DNA chip technology is a new genomic selection tool, which has been used to identify key genetic markers (single nucleotide polymorphisms) in pedigree selection programs. Genomic information is particularly helpful when selecting for sex-limited traits. Also, new measuring techniques, such as computer tomography to produce whole body reconstructions of broilers in three dimensions, have been included as one of the selection criteria. Primary breeding companies publish management guides for breeder and commercial broilers with standards of expected performance.
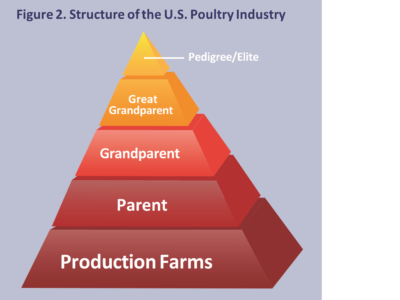
Genetic improvement of commercial broilers is achieved by using a production pyramid. A representative genetic pyramid illustrating production of broiler breeders is shown in the following figure. Primary breeders consist of pedigree, great grandparent, and grandparent generations that are owned by primary breeder companies. Eggs from pedigree flocks are hatched to produce great grandparent flocks, eggs from great grandparent flocks yield chicks for the grandparent generation. Grandparents consist of male and female lines, both of which are 2-way cross hybrids. Day-old chicks from male and female line grandparent stock are shipped to franchise hatcheries world-wide to create parent breeding flocks. Breeding the male and female parent lines together results in a 4-way cross broiler chicken. Primary breeder flocks are maintained under the highest level of biosecurity possible because of their value and critical importance in the production pyramid (Figure 2).
Live weights and feed utilization of commercial broilers have steadily improved over the last 50 years and over 90% of this improvement can be attributed to genetic changes. However, optimal nutrition, disease control, and environmental conditions must be provided for broiler chickens to reach their genetic potential.
Selection for rapid growth over many generations has reduced the ability of broiler breeders to produce high quality eggs in large numbers. A strong negative correlation between rapid growth and reproductive efficiency has resulted in broiler breeder hens with lower peak egg production and a shorter duration of lay than egg-type chickens. In addition, a positive correlation exists between high growth rates and multiple ovulations. Multiple ovulations result in eggs which are unsuitable for incubation because of double-yolks and thin or soft shells. Maintenance of fertility, hatchability, and egg production are important issues in the broiler breeder industry.
Parent Breeders
Parent breeding flocks are typically owned by commercial broiler companies. Eggs produced by parent flocks are transported to company-owned hatcheries. Chicks from these hatcheries are taken to commercial farms that are owned or contracted to the company. The chicks are raised as commercial broilers, slaughtered in company-owned processing plants, and marketed for human consumption. The relationship between primary breeders, parent breeders, and commercial broilers is illustrated in the Figure 3 below.
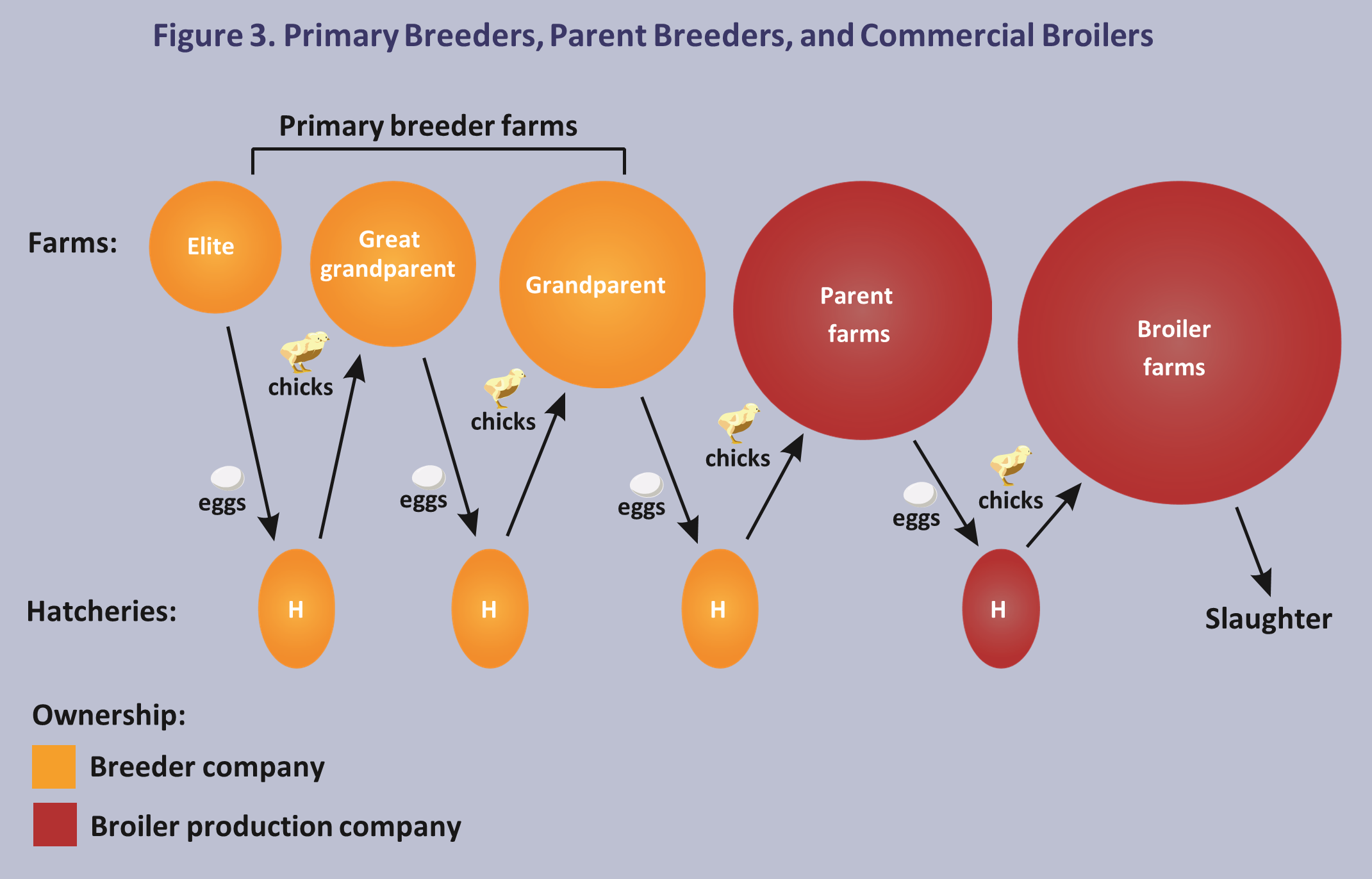
Breeder Houses
In a typical breeder house, 2/3 of the floor is covered by wooden or plastic slats located on each side of the house and the center 1/3 of the floor consists of a litter-covered scratch and breeding area in the center of the house. Slat and litter houses allow for a higher stocking density, which reduces the housing cost per bird. Rows of automated mechanical nests are located on the slats near the edge of the scratch areas on each side of the house. Slats extend beyond the front of the automated nests and waterlines and female feeding lines are placed over the slats. Fewer eggs are laid on slat and litter floors than on all-litter floors, especially in houses with mechanical nest systems. Floor eggs should not be set because they are heavily contaminated with bacteria on the surface of the shells. Bacteria can invade the eggs, multiply, and potentially cause eggs to explode, which contaminates the incubator. In addition, a relatively high percentage of floor eggs may be broken, destroyed, or eaten). Most droppings are collected in an area beneath the slats which helps maintain the quality of litter in the centrally located scratch area. Temperature in the breeding house should be maintained between 59°F and 77°F.
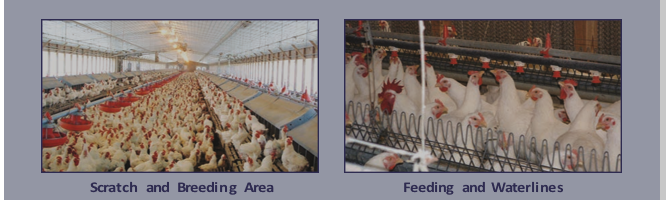
Biosecurity is higher on breeder farms than it generally is on commercial broiler farms, but it is not as stringently applied as on primary breeder farms. Breeder farms play a critical role in the operation of an integrated broiler company. Loss of a breeder flock to disease is not only costly, but loss of projected production from that flock makes losses much greater.
Photostimulation
Environmentally controlled rearing (“pullet”) houses need to be lightproofed so light intensity is less than 0.5 lux (0.05 foot-candles) when lights are off. Fans and air inlets are covered with light traps to exclude natural daylight; all light is supplied by electric lighting.
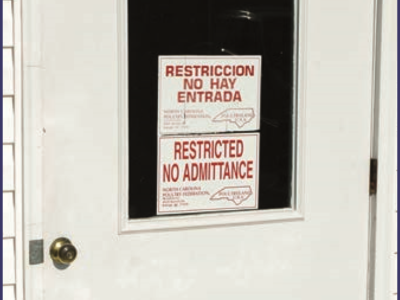
Black-out pullet houses allow farm managers to control the age of sexual maturity by conditioning the brain to respond to subsequent stimulatory long day lengths. Chickens do not initiate testicular and ovarian development until they are exposed to increased day length and light intensity. Light-proof pullet housing makes it possible for farm managers to improve flock uniformity by delaying light stimulation until a high percentage of pullets in a flock are physically and reproductively mature. If the flock is provided sufficient feed at the time of photostimulation to support both maintenance and egg production, small hens not producing eggs consume more feed than required for maintenance and become overweight prior to onset of egg production. Ultimately, they will produce fewer eggs with reduced fertility and hatchability.
Flocks stimulated at older ages have a greater percentage of hens with mature reproductive systems than flocks stimulated at younger ages. Males and females are reared on the same lighting program to ensure both sexes reach sexual maturity at the same time. A lighting program for broiler breeder chickens reared and producing eggs in light-controlled houses is given below from the Cobb Broiler Breeder Management Guide (2008).
Table 3. Cobb Broiler Breeder Management Guide (2008) |
||
Age(weeks) |
Light (hours) |
Light Intensity (lux) |
1 - 3 |
Gradual decrease from 24 hours at Day 1 to 8 hours by 14-21 days |
Gradual decrease from maximum light (>20 lux) to 20 lux by Day 7 |
3 - 20 |
8 |
5 - 10 |
20 - 21 |
11 |
40 - 60 |
21-22 |
13 |
40 - 60 |
22-23 |
14 |
40 - 60 |
23-60 |
15 |
40 - 60 |
Mating
Males and females are transferred from the pullet farm to the production farm between 18 and 23 weeks of age. Broiler breeders reproduce by natural mating. Unlike commercial turkeys, artificial insemination is not used. Flock or mass mating allows a number of males to mix with an entire flock of hens. Management practices to enhance mating efficiency include feeding programs to control body weights in female and male broiler breeders and maintenance of an optimum male:female ratio in the breeding flock. The recommended gender ratio is about 10 males per 100 females. Initially, eight males per 100 pullets may be better to reduce male aggression toward hens and other males, reduce female mortality, and encourage hen receptivity.
Mating frequency of males is estimated to be 5-40 times per day. Mating frequency of hens is estimated to be about 0.5 to 1.0 per day. Broiler breeder male fertility is high (more than 95%) until approximately 40 weeks of age, but declines thereafter because of reduced rooster mating frequency, lower percentage of live sperm, and the need for hens to mate more often to maintain fertility. To compensate for a decline in mating activity, spiking or intra-spiking of the flock with new males is used to stimulate male interest in mating. Beyond 65-70 weeks of age, fertility drops to low levels and the flock is sold.
Spiking consists of adding new, younger roosters to a flock to compensate for a decline in fertility, which generally occurs after 40-45 weeks of age, but can occur anytime and may occur more than once. During the first 6 weeks after spiking, increased mating is primarily due to old males that are stimulated by the presence of the young males. After 6 weeks, increased mating is due to activity of the young males.
For the first week after spiking there is an increase in male aggression with elevated male mortality and sexual interference (males preventing other males from mating). The result is approximately 12 weeks of increased or sustained fertility. During the first week after spiking, fertility declines slightly due to male aggression and mating interference but significantly increases by 2 weeks post-spiking.
Bringing new males into the flock creates a biosecurity risk. Intra-spiking overcomes this problem by exchanging males of the same age between houses on the same farm or between pens in the same house. Intra-spiking males are stimulated by encountering new hens and begin to mate immediately. Aggression and sexual interference increase for the first two weeks after intra-spiking but there is no significant increase in mortality from either the original males or spiked males. Double intra-spiking is possible and may help maintain higher levels of hatchability for up to 15 weeks.
Feeding
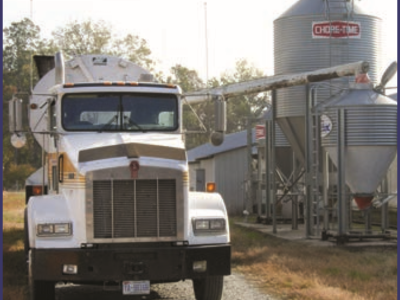
Controlling body weights of both males and females during rearing and egg production is a critical factor in determining their performance in the breeder house. Males and females are typically grown separately during the rearing period, as target body weights are different. Attaining target body weights as breeders age is achieved by regular adjustments of feed allowances based on weekly body weight measurements of chickens in the flock.
Deviations from target body weight curves require adjustments to feed allocations that can be maintained or increased, but never decreased from day 1 of age until peak egg production at around 30 weeks of age. On days 7 and 14 after placement, 10 birds can be weighed together in a bucket. Thereafter, birds should be individually weighed at the same time on the same day of every week before feeding. Onset of sexual maturity is influenced by body composition, so males and females must have both correct body weights and correct body composition at the onset of lay. At the onset of lay, the females’ body should have an adequate fat reserve as well as adequate muscle mass. Goals of a typical broiler breeder feeding program are shown in the table below.
Table 4. Goals of a Typical Breeder Feeding Program |
|
Broiler Age Range |
Feeding Program Goals |
Day 1 - 4 weeks |
Feed ad libitum |
4 - 16 weeks |
Control body weight by providing sufficient nutrition for growth and maintenance while preventing birds from becoming overweight by small, regular feed increases. |
16 - 23 weeks |
Accelerate bodyweight gain and promote rapid development of ovaries and testes in preparation for egg production by increasing the feed allocation |
23 - 30 weeks |
Meet demands of growth and egg production while avoiding excessive weight gain with small, frequent feed increases. |
30 - 70 weeks |
Avoid excessive weight gain after peak egg production has been reached and physical growth has ended by slowly reducing feed for females based on bodyweight and egg weights. |
Females
Overfeeding broiler breeder hens leads to development of abnormal ovarian structure, reduced egg production, impaired fertility, increased hen mortality, and increased frequency of defective eggs. At the onset of lay, overweight pullets have a tendency to develop multiple large yellow ovarian follicles (“superovulation”), each of which produces progesterone. Superovulation results in excessive progesterone production, which triggers multiple concurrent ovulations.
Multiple ovulations result in regular eggs or large eggs containing double yolks, which have no shell, soft shells, or thin shells. These defective eggs have poor embryo viability and poor hatchability and are not suitable for incubation. Multiple ovulations also may result in laying more than one egg per day, abdominal laying, and laying eggs at abnormal times in the day (erratic ovipositioning). In addition, overweight hens are too large to breed effectively and tend to have sperm storage and sperm transport problems because of fat infiltration into sperm storage glands at the shell gland-vaginal junction of the oviduct.
Optimum ovarian function is one ovulation per day, which can be achieved by feed restriction. Feed restriction during rearing, breeding, or both reduces the weight of the ovary and number of large yellow follicles at sexual maturity, erratic ovulation, and defective eggs.
Additional benefits of restricted feeding include reduced mortality and lower feed costs. Reproductive performance of broiler breeder hens on restricted and ad libitum feeding programs is documented and compared in the table below (International Hatchery Practice, Volume 20, No. 1, page 7, 2009).
Table 5. Broiler Breeder Hens (0 to 60 Weeks |
of Age) |
|
Ad libitum |
Restricted |
|
Body Weight (lbs.) |
11.7 |
8.2 |
Mortality (%) |
46 |
4 |
Egg Numbers |
58 |
157 |
Hatch of Eggs Set (%) |
43 |
86 |
Feed Intake (g/day) |
||
0 - 24 weeks |
163 |
63 |
24 - 37 weeks |
192 |
157 |
37 - 60 weeks |
142 |
151 |
No. Yellow Follicles |
13.5 |
7.3 |
Males
Achieving male body weight targets that closely adhere to growth curve recommendations by primary breeder companies is the single most important factor in attaining high flock fertility. Male growth and breast muscle development must be controlled, especially during the first 16 weeks of life when skeletal size is largely determined. Overfeeding broiler breeder males causes excess body weight and excessive development of breast musculature, both of which impair mating efficiency.
Fertilization requires semen transfer from males to females by copulation. Excessive pectoral muscle creates an imbalance so overweight roosters have difficulty making cloacal contact with hens and transferring semen. Furthermore, excessive body weight is associated with development of foot pad and leg problems, which negatively impact the mating process and occur in more than 30% of broiler breeder males.
Sertoli cells protect developing sperm cells and proliferate between 2 and 12 weeks of age, not thereafter. Numbers of mature sperm produced is limited by the number of Sertoli cells, so maximum potential for sperm production is established by 12 weeks of age. From 16 to 23 weeks of age, nutrition must be sufficient to support maintenance, growth of testes, and production of reproductive hormones. Appropriate levels of follicle stimulating hormone and luteinizing hormone are critical for testes development and establishing a “feedback loop” between the brain and the testes.
Feeding programs should allow males to increase their body weight gradually throughout the breeding period.
Body weight gains should be limited to small, consistent amounts to prevent excessive breast muscle development. Male body weight loss will immediately result in diminished sperm production and decreased mating activity, so weight loss must be avoided.
Production Phase
Males need to be transferred to the production house 3-5 days earlier than the females, so they can learn to eat from the male feeder. After males and females are mixed, separate feeding systems are available so body weight and uniformity of males and females can be independently controlled. It is important that males do not have access to the females’ feed and vice versa. As roosters have larger heads than hens, males can be kept out of female feeders by exclusion systems such as grills or roller bars. Grills placed over hen feed troughs create vertical and horizontal restrictions which exclude males with greater head width and full combs, but allow females unimpeded access to the feed.
With some strains of broiler breeders, the difference between the size of the heads or combs between males and females is insufficient to control feed access with grills. In these cases, a plastic bar, commonly called a “nose bone” is placed through the nares and nasal septum. Male feed lines need to be sufficiently elevated above the floor to prevent hens from reaching feed intended for roosters. In some housing arrangements a separate male water line runs down the scratch area, but, more commonly, the males use the female water lines above the slates.
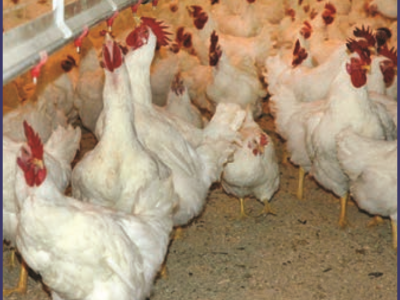
Ideally, breeders should be fed daily, but skip-a-day feeding programs have been used when feeding space is limited and are most common. Broiler breeders consume their feed in a short period of time (less than 30 minutes). Consequently, feed should be distributed to all chickens along the entire length of the feed line in less than 3 minutes so all birds can eat at the same time. If delivery takes too long, aggressive birds consume most of the feed as it leaves the hopper.
If feed is not delivered along the length of the entire feed line in a short period of time, dominant birds have access to more feed and gain more weight each week than smaller, less dominant birds. Under these conditions, body weight uniformity declines even if initial body weight uniformity was good. Another problem that can occur with skip-a-day feeding is engorgement of food to the point that birds can compress the trachea and die of suffocation. When birds are seen in respiratory distress shortly after feeding, the crop needs to be checked to see if it is hard. If so, the bird can usually be saved by gently massaging the food laterally away from the trachea.
Hatchery
Hatcheries should be built in isolated locations away from feed mills, processing plants, or industrial buildings, which may produce contaminated dust or pollutants. Fences with a gate and a guard erected around the hatchery and decontamination equipment, showers, and change rooms for employees would provide maximum biosecurity, but currently are not common in the US. Separate rooms should be provided for the office, fumigation, egg grading, egg holding, setters (incubators), hatchers, chick grading and boxing, chickholding, supplies, and waste disposal. Central fogging systems, which provide a timed release of disinfectant mist from high pressure nozzles, should be located throughout the hatchery, including the setters and hatchers.
Strategically located high pressure hot water outlets enhance sanitation efforts, and walls and floor surfaces should constructed of durable, easy to clean materials. Floors slope toward drains, which are trapped to prevent blockages. Each room should have its own ventilation system and air pressure in each room should be adjusted so that the cleanest rooms have the highest positive pressure.
Hatchery work and egg flow patterns contribute to biosecurity, as do placement of ventilation inlets and exhausts. The hatchery should be divided into clean and dirty areas, which must be separated to avoid cross contamination. Hatching eggs should enter one end of the building and chicks should leave from the other end.
Ventilation systems should move air from clean areas to the dirty areas, in the same direction as hatching eggs move from setters to hatchers. Air pressure differences among the areas in the hatchery help minimize backflow of contaminates into clean areas. Ventilation systems need frequent inspection a nd periodic cleaning.
Egg Collection, Selection, Storage, and Pre-Warming
Development of the embryo begins at the time of fertilization in the infundibulum of the oviduct and proceeds as the egg is formed until ovipositioning. As the egg cools, the rate of embryo development slows and it enters diapause. Careful handling of the egg is necessary to preserve the integrity and viability of the early embryo prior to incubation and further development.
Eggs should be collected at least 3 times per day in normal temperatures and 5 times per day when temperatures are above 85°F. Frequent gathering reduces the probability that eggs become contaminated with bacteria from feces or nest materials, and prevents overheating of eggs in summer and chilling of eggs during winter. Clean nest eggs should be collected first and submitted to the hatchery for incubation. Dirty nest eggs, cracked eggs, and floor eggs depress hatchability and should be collected and packaged separately. These eggs are not suitable for incubation. Most contamination in hatcheries originates on the breeder farm.
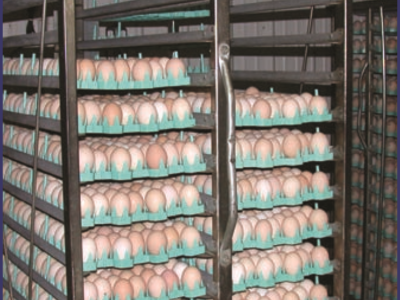
Egg selection is used to eliminate eggs that are less likely to hatch and produce quality chicks. Egg size is a selection criterion since unusually large or small eggs do not hatch as well as medium-sized eggs. Overweight and underweight eggs can be removed by automated equipment. Round or elongated eggs and eggs with thin or wrinkled shells do not hatch well and should not be sent to the hatchery. Dirty eggs may be contaminated with yolk, dried blood, or feces and these should be removed and discarded.
Eggs are moved into an air-conditioned egg room for storage until they are picked up and taken to the hatchery. They should be held in storage on the farm for as short a time as possible. After being picked up from the egg room on the breeder farm, they are placed in an egg holding room in the hatchery and stored there until they are incubated. Each day of storage adds one hour to the time required for incubation, so fresh and stored eggs should be set at different times.
Diffusion of carbon dioxide and water vapor from the egg through pores in the shell contributes to loss in hatchability during storage. After 6 days of storage, hatchability declines by approximately 0.5 to 1.5% per day. Eggs should be cooled to below 75.2°F and held at 75-80% humidity in the storage room. Cooling eggs below physiological zero for broiler breeder eggs (75.2°F) minimizes embryo development during storage. The longer eggs are held in storage, the lower the recommended storage temperature.
Pre-warming eggs prior to setting is advisable to avoid temperature shock to the embryo and prevent condensation of moisture on the external surface of the egg’s shell (egg sweating). Eggs may sweat when transported from a cold storage room on the farm to a warm hatchery or from a cold storage room in the hatchery to the setter room of the incubator. Eggs need 6 to 18 hours for pre-warming and good air circulation should be provided during the pre-warming period. A dedicated pre-warming room should provide a temperature of 73°F and 45% relative humidity.
Setter (Incubator)

Incubation involves bringing fertile eggs to hatching by natural or artificial means. Artificial incubation frees breeding hens from the necessity of incubating eggs so the hens can continue to produce eggs. Five well-known environmental factors impact embryonic development – temperature, humidity, ventilation, egg turning, and egg orientation. An incubator in a commercial broiler hatchery is shown in the photo on the right.
The recommended temperature for setters is 99.5 – 100°F in multi-staged machines. Later in incubation, embryos are relatively resistant to cooling. In contrast, overheating can cause malformations, malpositions, or may be lethal.Malformations may include exposed brains, missing eyes, beak or face abnormalities, or viscera outside the body cavity. All setters
have hot spots and cold spots, and care should be taken that embryos in hot spots are not subjected to heat stress. In single-stage incubation, temperature can be reduced to compensate for the heat produced by growing embryos.
Relative humidity in setters should be 50-60% depending on manufacturer’s recommendations. Water vapor is lost through the pores of the shell. Egg weight decreases because of water loss during incubation. While most animals try to conserve water, bird eggs must lose water during embryonic development to facilitate hatching. Metabolic water generated by the embryos must diffuse through the shell to maintain the relative water content of incubating eggs. A fresh egg should lose approximately 12% of its weight by 18 days of incubation due to loss of water from the egg. Loss of moisture during embryonic development allows the air cell to enlarge and occupy 1/3 of the egg by 19 days of incubation.
Ventilation in the setter must support embryonic respiration by providing an adequate supply of oxygen and removing excess carbon dioxide. The average chicken egg has around 10,000 pores, which allow oxygen and carbon dioxide to move through the shell by diffusion. Fresh air entering the setter contains 21.6% oxygen. If fresh air is dry and supplies little moisture, it may be necessary to humidify air in the room containing the setter; conversely, if ambient humidity is high, it may be necessary to dehumidify the air before it enters the incubator. Exhausted air leaving the setter removes water vapor, carbon dioxide, and excess heat. Carbon dioxide levels in the machine should not exceed 0.4%, as embryos can die if carbon dioxide levels become too high
Turning eggs in the setter on a regular schedule assists in the development of extra-embryonic membranes and aids in temperature control. In modern hatcheries, turning devices rotate eggs 90 degrees and are equipped with timing mechanisms so eggs are turned every hour. It is extremely important that eggs be placed in the setter with the large end up.
Hatcher
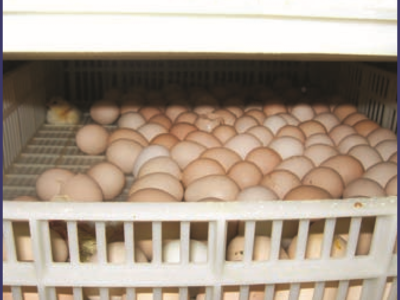
Hatchers are kept in a separate room to isolate the down, egg debris, and micro-organisms generated during hatching from the rest of the hatchery. Hatchers have chick-holding trays where eggs are laid on their sides to allow free movement of chicks out of the shell at hatching.
After 18 days of incubation, eggs are removed from the setter, vaccinated, and transferred to the hatcher. Eggs may be candled to identify and remove infertile eggs and dead embryos so live chicks are not exposed to these potential sources of pathogenic bacteria after hatching. In ovo injection systems are routinely used for administration of vaccines to protect broiler chickens against Marek’s disease, infectious bursal disease, and fowl pox.
Vaccination in ovo requires far less labor and time and is less stressful to the chicks than subcutaneous administration of Marek’s disease vaccine. In ovo vaccination machines can vaccinate 60,000 eggs per hour while consistently delivering the correct dose to the correct location in the embryo. Chicks vaccinated in ovo can be moved out of the hatchery without delay, which reduces the time between hatching and access to feed and water in the brooder house.
Most broiler hatcheries hatch twice a week from each hatcher. The hatcher is cleaned and disinfected between hatches. Hatchers must be dry and up to proper temperature before receiving hatching eggs. Moisture must be adequate to ensure that shell membranes remain soft and pliable so chicks can escape from the eggs. Additional moisture may be supplied by a spray system. Temperature is slightly lower than the setter (98°F) to avoid overheating and the relative humidity of around 70% is higher than the setter.
The hatch window is the period of time when chicks emerge from the eggs. Chicks peck the inside of the eggshell until the shell is sufficiently broken to allow chicks to escape from the egg, a process called pipping. Internal pipping occurs a couple days before hatching when the beak of the embryo penetrates the air cell. Variability in hatching time is to be expected from chicks in a single setting because eggs in a hatch may differ in storage time and storage conditions, environmental conditions within the same setter or hatcher, age of breeder flocks supplying the eggs, shell characteristics, and original egg size.
Eggs that hatch too early are susceptible to dehydration, which may result in increased early chick mortality and poor broiler performance. Eggs that hatch too late have poor hatchability, impaired chick quality, increased numbers of pipped but unhatched eggs, and increased numbers of unhatched eggs that contain live embryos.
Pulling the hatch refers to removing chicks from the hatcher. Chicks should be removed when most are dry and fluffed up but while around 5% are still damp on the back of their necks. Removing chicks from the hatcher too soon results in “green chicks” that are still wet, susceptible to chilling, or have open navels that provide entry points for bacteria. Excessive dehydration, elevated mortality after placement, and reduced growth and flock uniformity occur in chicks that remain in the hatcher too long.

Chick processing
After being separated from hatching tray debris, chicks are graded into first quality or culls. Chicks that possess anatomical deformities, partially closed navels, crooked toes, excessively wet down, or twisted legs are culled.
The gender of day old chicks can be determined by feather sexing or vent sexing. Feather sexing is based on the length of the primary and covert feathers on the wing. The top row of feathers is composed of the coverts and the bottom row of feathers are primary feathers. In females carrying fast feathering genes, coverts are always shorter than primaries. Males carry slow feathering genes, so covert feathers are always as long as primary feathers. Vent sexing involves examination of the cloacal wall to detect rudimentary male copulatory organs.
Spray vaccination of day-old chicks in the hatchery is a commonly used for mass administration of vaccines against Newcastle disease and infectious bronchitis. Aerosolized vaccine viruses contact mucous membranes of the nasal passages, trachea, and lungs and stimulate both local and systemic immunity. In addition, coccidiosis vaccines may be administered by a spray, which settles over the down on chicks and is subsequently ingested.
Chicks are sorted, counted, and placed into chick boxes before being moved to the chick holding area.
Chick Holding and Transport to Farms
After being placed into chick boxes, chicks are moved into the chick holding room where the flock to be delivered to the farm is assembled. It is common for flocks to have a hundred thousand or more chicks. The chick holding room at the hatchery should have a temperature of 75°F and relative humidity of 70%. These conditions are close to the chicks’ thermo-neutral zone at which they are comfortable. Chicks are delivered to the farm in specialized vehicles equipped with heating, cooling, and ventilation systems to control the chick’s environment. Chick delivery drivers are well trained and keep a log book, which records the time the truck leaves the hatcher, all stops, and time of arrival at the farm. The vehicle cab has a display showing the transport conditions.
Waste Disposal and Cleaning
With 85% hatchability, 15% of eggs will be infertile or contain dead embryos. Hatchery waste includes infertile eggs, dead embryos still in the egg, down, shell fragments, dead chicks, and cull chicks. Waste disposal may occur by incineration or hatchery waste may be processed into livestock food known as hatchery by-product. Cleanup after pulling the hatch, processing chicks, and holding chicks is critically important.
A Material Safety Data Sheet should be on file for each disinfectant used in the hatchery and eyewash stations should be available for employees inadvertently exposed to chemicals. Microbiological monitoring using swabs or culture plates should routinely be used to monitor the level of contamination in a hatchery. Critical areas for sampling include egg room air, air inlets of each setter and hatcher, inside each setter, vaccination room air and surfaces, vaccine and diluent samples, chick room air, and chick processing equipment surfaces.
Automation
Automated hatcheries may hatch more than two million chicks per week and have shorter throughput times, which promote chick quality. Automation provides gentler handling of eggs, more precise vaccination, more accurate chick counting, and a better working environment for employees. Fully automated hatcheries require less labor, only one employee for every two million chicks hatched per year.
Computer-controlled machines are available to grade eggs before setting and to monitor and control temperature, humidity, carbon dioxide, and egg turners in each setter. At 18 days of incubation, automated machines will candle eggs, perform in ovo vaccination, and transfer eggs to the hatcher. After hatching, machines can separate chicks from broken shells and hatching debris, count and weigh chicks, vaccinate with in-line sprayers, place chicks in boxes, and remove debris from the hatchery.
Reference: "USDA APHIS | FAD Prep Industry Manuals". Aphis.Usda.Gov. 2013. https://www.aphis.usda.gov/aph...
The manual was produced by the Center for Food Security and Public Health, Iowa State University of Science and Technology, College of Veterinary Medicine, in collaboration with the USDA Animal and Plant Health Inspection Service through a cooperative agreement.